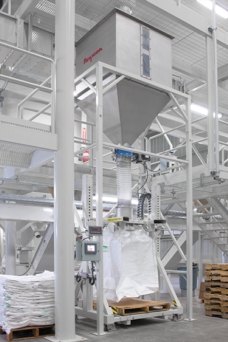
Oprima para ampliar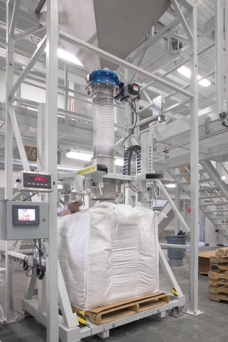
Oprima para ampliar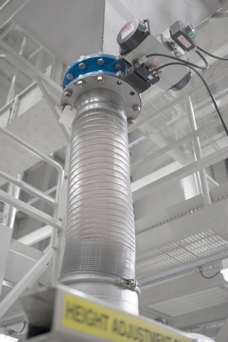
Oprima para ampliarEl arroz desciende de la tolva, por medio de una válvula de domo y se descarga descendentemente en el llenador de supersacos TWIN-CENTERPOST™.
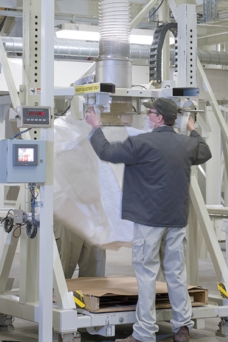
Oprima para ampliar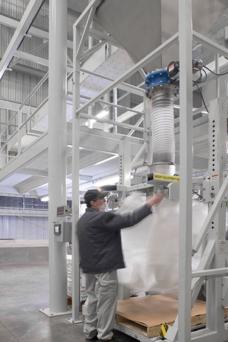
Oprima para ampliarEl operador sujeta los lazos del saco a los ganchos retráctiles de sacos que suspenden el saco durante el llenado.
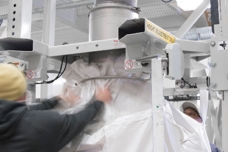
Oprima para ampliarLa boca del saco se jala sobre un collar inflable el cual junto con una ventila de desplazamiento de aire filtrado asegura el llenado libre de polvo.

Oprima para ampliarEl operador infla el saco, eliminando los pliegues antes del llenado.
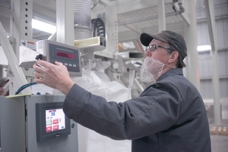
Oprima para ampliarUna vez que el operador conecta el saco y presiona el botón de inicio, un PLC automatiza el proceso de llenado, cerrando la válvula de domo cuando el saco alcanza su peso objetivo.
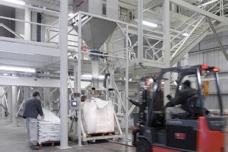
Oprima para ampliarEl montacargas retira el saco lleno en la plataforma mientras que el operador prepara otro saco para su llenado.
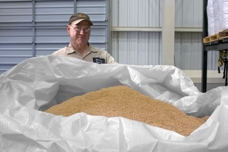
Oprima para ampliarUn supersaco de arroz blanco y pulido está listo para enviarse. El llenado está diseñado para cumplir con la creciente demanda de supersacos de Kennedy Rice.